目次
【メリット①】成形不良が徹底的に低減された金型製作が可能
弊社関東製作所では、製品設計の段階から、成形不良を極力抑えた形状の提案が可能です。
射出成形には『ヒケ』や『反り』などの不具合は必ずついてまわり、金型を製作する前に、それら不具合が起こりにくい金型設計を行うことが、コストダウンや納期短縮に大きく貢献します。
30年以上『金型&成形』に従事してきたベテランスタッフが、お客様が構想する製品を、樹脂成形に最適化された金型設計へと導きます。
> 射出成形における『成形不良の発生原因とその対策』記事一覧へ
また、ベテランの経験則だけで金型設計への落とし込みを完結しないのが弊社の強みです。流動解析ソフトを用いて、モニター上で金型内での樹脂の流れ・不具合発生をシミュレーションし、客観的なデータをもとに製品形状を確定させます。
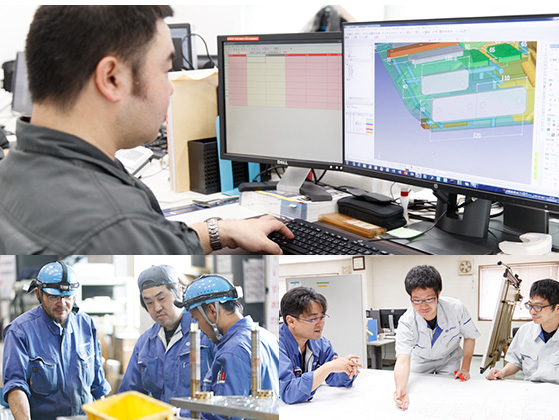
関東製作所グループは『ベテランスタッフの経験値』『流動解析による客観的データ』その両方を組み合わせます。
これが弊社が射出成形において、プロジェクトのコストダウンや納期短縮の実現を可能としているエビデンスなのです。
【メリット②】スピーディーな金型仕様の決定!ポンチ絵を描きながらの打合わせ
弊社射出チームのスタッフは、各々が『金型』『成形』両方にお応えできるので、両者を加味した提案力が強みです。
弊社スタッフ:「このリブの太さだと底板がヒケますよ。」
お客様担当者:「ここは強度が欲しい箇所。ヒケてもいいからこの太さは確保したい。」
弊社スタッフ:「なるほど。では外観のシボは深めにして逃げましょう。」
まだお客様側で具現化できていない構想も、ぜひ弊社にご相談下さい。上記会話のように、打合わせの場においてどんどん仕様が確定していくと、プロジェクト自体も非常にスピーディーに進みます。
さらに弊社スタッフは、打ち合わせの場で『ポンチ絵』を書きながら話を進められます。頭の中のイメージがその場で絵として具現化すると、お客さまもきっと判断が明確になるでしょう。
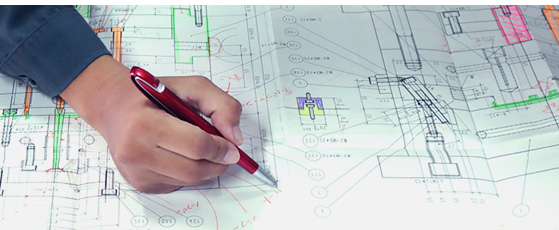
【メリット③】効率的な生産ラインを見据えた金型製作が可能
例えばウォッシャータンク等の中空品は、射出成形の場合、専用の熱溶着機で製品同士をくっつける必要があります。弊社には、プラスチック成形品の『後加工専用機』の製作部門があるため、その熱溶着機も抱き合わせで製作が可能です。
金型から後加工用の専用機械まで一社内で製作できるということは、量産工場において、ライン単位での設計提案が可能となります。
①弊社製作の金型で樹脂成形を行う。
②成形された製品を、弊社製作の『熱溶着機』にセットし溶着する。
③出来た製品を弊社製作の『検圧機』にセットし検査。
金型での成形品の生産から良品の保証まで完結。この一連の生産ラインを、弊社だけで提案できるのです。
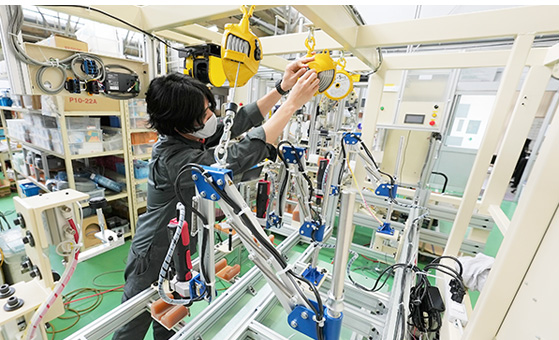
ライン単位で設計できるということは、
- 成形された成形品の取出しの向きを考慮して、金型内での製品レイアウトを決められる。
- 溶着機に製品を固定するために、金型内に固定用のリブを前もって設計しておく。
など、金型製作単体で進めた場合では決して気付かない『仕様』を、金型に織り込むことが出来るのです。
このように、金型設計から樹脂成形、そして品質保証まで社内一貫で提供できることは、お客様にコスト面や納期スケジュールで大きく貢献できると自負しております。その為の人的リソースや設備環境は潤沢に整えております。